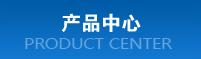

罗茨风机停机故障原因_罗茨鼓风机
罗茨风机停机故障原因:如何防止罗茨鼓风机负载突然停机?
罗茨风机负载停机有很多中原因,如:电线短路、叶轮卡死、机壳变形、轴承损坏等,都可能造成罗茨风机出现停机的情况,如何防止罗茨风机突然停机,其实只有一个方法,就是注重“平时养护”,防患于未然。
为了防止罗茨风机突然停机,我们在平时养护时,需要做到以下几点:
1、经常检查电机的线路,查看是否有出现破损短路的情况,防止因电线老化造成的罗茨风机停转。
2、注意罗茨风机出现的异常现象,如:高温、超压、异常噪音等,这些现象下面,可能暗藏着罗茨风机的故障。罗茨风机养护一二
3、定期大检查,定期大检查还是很有必要的,半年一次大检查即可,能够让我们及时发现罗茨风机的故障,同时也能排除一些潜在小故障。
罗茨风机负载突然停机,如何降低最小伤害?罗茨风机有个很重要的配件,就是逆止阀,安装在管道内部,如果您对逆止阀的工作原理不懂,可以查看下这篇文章:逆止阀的工作原理动画,通过这篇文章,我们可以看到,逆止阀能够保护我们的风机不受反流气体的损坏,如果没有逆止阀,在停机的情况下,罗茨风机叶轮回转可能会被打坏。
当我们不能防止罗茨风机突然停机时,我们可以使用逆止阀,来保护罗茨风机受到最小的伤害,罗茨风机倒转的危害在之前的文章中,锦工风机小编也说了很多了,有兴趣的朋友可以点击前面的链接进行查看。
有些时候,罗茨风机突然停止转动,是我们意料不到的,如:轴承损坏、叶轮抱死、齿轮损坏等,这些故障需要对风机进行拆卸才能够检测到,所以,有些时候,我们只能凭借罗茨风机的反应进行判断,罗茨风机是否要出现故障,举个例子:如果我们的叶轮或者轴承出现了损坏,罗茨风机在运行时,我们可以听到有异常的杂音,还有可能存在剧烈的振动,一旦发现此类现象,立刻停掉电源对风机进行检查,这样便能防止更大的损失了。
如果您有罗茨鼓风机的采购问题,可以联系我们的官方客服热线
文章
>>摩洛哥客户抢购锦工特价罗茨鼓风机第一单!
>>罗茨鼓风机选型是如何选的?看论坛中各位大神的选型方法!
>>3分钟让您学会如何高效使用罗茨鼓风机!使用方法技巧!锦工风机
>>我知道您也想要这样一款“特价罗茨鼓风机”
>>罗茨鼓风机在气力输送时重点检查哪些内容?
罗茨风机停机故障原因:山东锦工机械有限公司
1、故障分析与处理:查看变频器参数,罗茨风机变频器的加速时间为15秒、减速时间为15秒,由于改造之前变频器运行正常,频率上调和下调都正常,改造之后出现异常,电气维护人员与装置机械专业的人员沟通后发现,风机和电机的链接由原来的皮带传动改造为轴传动,改为刚性连接,罗茨风机在降速过程中,惯性很大,在变频器的输出频率很快降下来的情况下,而风机仍然以较高转速在运行,出现“倒发电”状态,造成变频器直流环节过电压,为避免这种情况的出现,必须将变频器的减速时间放大,使之能够与罗茨风机转速调整过程中的机械惯性匹配,从而避免出现报警或停机现象。
罗茨风机停机故障原因:网站首页|关于我们| 产品中心| 案例展示| 新闻资讯| 常见问题| 销售网络| 联系我们|
罗茨风机故障原因,为什么不转了的原因,案例分析
罗茨风机为什么不转了呢?都是些什么故障原因导致罗茨风机不转了呢?罗茨风机是运转类机械设备,使用中遇到故障不转了的原因有哪些?接下来我们一起来看看故障原因及解决办法。
罗茨风机故障不转了的原因:
1、检查电压或过热跳闸、是否未接通电源、线路中断、接线不良或保险丝断了等原因,需要检查维修并接通电源。
2、检查电机损坏不工作,绝缘不良或灰尘太多,进水等问题,检查电机接线或更换电机。
3、轴承损坏:轴承润滑不良或搬运碰撞导致转子靠偏,或间隙增大等损坏情况,(需要懂机械的或维修人员)拆卸进行专业维修。如维修有难度,及时找专业的风机生产厂家来指导维修或更换。
4、空气滤清器堵塞、排气管道堵塞,及时清理或进行必要的更换。
5、风机中有异物卡死,灰尘或杂物混进太多,及时清理。
6、风机生锈问题,进水或长期不用(未防潮)导致生锈,需要加入适量洁净的汽油,进行润滑,并用手动转动两到三圈润滑。
关于罗茨风机工作原因,在这里举例说明一个:
一、沈阳案例:输送介质杂质导致风机不转的原因如下:
沼气使用罗茨风机或碳酸钙使用罗茨风机出现输送介质含杂质较多,粘附在叶轮上,造成叶轮间隙变小,这是就出现故障了,挤住不转了。当时客户说,为什么会突然不转了呢,如果是风机的问题,会正常运转了一段时间后突然不转吗?这样的情况又该怎么来解决呢?
罗茨风机出现这种状况,需要用干净的热水冲洗叶轮,如果堵塞严重需要拆机解体清理叶轮,因此此类风机运行时建议注意风机周边环境卫生,尽量避免油污沾附太多杂质,导致风机运行不畅或卡死情况,也可定期用清水清洗叶轮,做到提前预防。特别是长时间停机前,一定要冲洗干净,并涂上适量的润滑油使风机 保持润滑状态,以防叶轮锈死,再启动时风机不转情况。
罗茨风机正常使用的维护要点,主要是保证物料空气的清洁度、润滑油保持及时有效的润滑及防止超温。
1、空气环境清洁:在空气清洁方面,除了注意风机周边环境以外,可采用海绵做过滤网,定期进行清理,并配合在检修时对风机内部的清洗,已能满足风机的清洁要求和生产要求。
2、定期规定检查内容为看、听、摸。看出口温度、压力和电流表显示是否超标,油位是否正常,是否漏油漏气,听声音是否有异常,摸轴承座及其他部位温度是否正常。
3、润滑部位在润滑方面,要保证润滑设施的有效性及润滑油的充足。齿轮箱采用68号润滑油,轴承和密封部位采用ZN-3润滑脂,每个部位保持0.2~0.5kg。
4、降温情况:风机在高温季节满负荷运行时,易出现整机超温(出口气温超过85℃),故障率徒增而风量下降。为此可以自行设计制作一个简易的水冷却装置,自上而下流经风机机壳表面以带走部分热量,达到降温目的,助风机安全度过高温季节。
罗茨风机的维护和日常保养还有更详尽的,后续会及时提供给新老用户。本身罗茨风机的规格型号也是较多的,以上只是提供一个真实案例,让大家大致了解一下,如需获得罗茨风机的更多技术需求,请进入到锦工风机官网技术顾问一直在线,将为您一对一提供技术参考或风机的更多。
罗茨风机停机故障原因:罗茨风机的常见故障及解决方法,已经总结好了
原标题:罗茨风机的常见故障及解决方法,已经总结好了
罗茨鼓风机是一种定容积回转式气体动力机械。气缸由机壳和两端墙板包容而成,一对相互“咬合”(因为有间隙,两叶轮并不直接接触)的叶轮将进气口与排气口分隔开来,通过一对同步齿轮的转动,两叶轮在气缸中作等速反方向旋转,在旋转过程中,进气口的气体不断的被叶轮推移到排气口,从而达到强制排气的目的。今天因大师将为大家介绍罗茨鼓风机常见故障及解决方法。
原因:
1)叶轮上有污染杂质,造成间隙过小;
2)齿轮磨损,造成侧隙大;
3)齿轮固定不牢,不能保持叶轮同步;
4)轴承磨损致使游隙增大。
解决办法:
1)清除污物,并检查内件有无损坏;
2)调整齿轮间隙,若齿轮侧隙大于平均值30%~50%应更换齿轮;
3)重新装配齿轮,保持锥度 配合接触面积达75%;
4)更换轴承。
原因:
1)安装间隙不正确;
2)运转压力过高,超出规定值;
3)运转温度过高;
4)机壳或机座变形,风机定位失效;
5)轴承轴向定位不佳。
解决办法:
1)重新调整间隙;
2)查出超载原因,将压力降到规定值;
3)检查安装准确度,减少管道拉力;
4)检查修复轴承,并保证游隙。
原因:
1)油箱内油太多、太稠、太脏;
2)过滤器或消声器堵塞;
3)压力高于规定值;
4)叶轮过度磨损,间隙大;
5)通风不好,室内温度高,造成进口温度高;
6)运转速度太低,皮带打滑。
解决办法:
1)降低油位或挟油;
2)清除堵物;
3)降低通过鼓风机的压差;
4)修复间隙;
5)开设通风口,降低室温;
6)加大转速,防止皮带打滑。
原因:
1)进口过滤堵塞;
2)叶轮磨损,间隙增大得太多;
3)皮带打滑;
4)进口压力损失大;
5)管道造成通风泄漏。
解决办法:
1)清除过滤器的灰尘和堵塞物;
2)修复间隙;
3)拉紧皮带并增加根数;
4)调整进口压力达到规定值;
5)检查并修复管道。
原因:
1)油箱位太高,由排油口漏出;
2)密封磨损,造成轴端漏油;
3)压力高于规定值;
4)墙板和油箱的通风口堵塞,造成油泄漏到机壳中。
解决办法:
1)降低油位;
2)更换密封;
3)疏通通风口,中间腔装上具有2mm孔径的旋塞,打开墙板下的旋塞。
原因:
1)滚动轴承游隙超过规定值或轴承座磨损;
2)齿轮侧隙过大,不对中,固定不紧;
3)由于外来物和灰尘造成叶轮与叶轮、叶轮与机壳撞击;
4) 由于过载、轴变形造成叶轮碰撞;
5) 由于过热造成叶轮与机壳进口处磨擦;
6) 由于积垢或异物使叶轮失去平衡;
7) 地脚螺栓及其他紧固件松动。
解决办法:
1)更换轴承或轴承座;
2)重装齿轮并确保侧隙;
3)清洗鼓风机,检查机壳是否损坏;
4)检查背压,检查叶轮是否对中,并调整好间隙;
5)检查过滤器及背压,加大叶轮与机壳进口处间隙;
6)清洗叶轮与机壳,确保叶轮工作间隙;
7)拧紧地脚螺栓并调平底座。
原因:
1)与规定压力相比,压差大,即背压或进口压力大;
2)与设备要求的流量相比,风机流量太大,因而压力增大;
3)进口过滤堵塞,出口管道障碍或堵塞;
4)转动部件相碰和磨擦卡住;
5)油位太高;
6)窄V型皮带过热,振动过大,皮带轮过小。
解决办法:
1)降低压力到规定值;
2)将多余气体排放出去或降低鼓风机转速;
3)清除障碍物;
4)立即停机,检查原因;
5)将油位调到正确位置。
:
河北罗茨鼓风机维修 品牌罗茨鼓风机报价 罗茨鼓风机优点
山东锦工有限公司
地址:山东省章丘市经济开发区
电话:0531-83825699
传真:0531-83211205
24小时销售服务电话:15066131928
