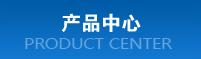

煤气净化 罗茨风机_罗茨鼓风机
煤气净化 罗茨风机:[填空题] 煤气净化运行时,净化设施与罗茨风机压差过大异常时,应首先判断设施内有()现象。
呼吸防护装备是防御空气污染物进入呼吸道的装备。()
响应时间指在规定条件下,从探测器接触被测气体到稳定指示值的时间,通常指读取达到稳定指示值90%的时间,即T90。()
煤气设施检修时,空间CO浓度在150PPm,检修人员连续作业时间不得超过()分钟。
主节点是下列()杆件紧靠的扣接点。 ["A、角杆","B、立杆","C、纵向水平杆","D、横向水平杆"]
焦炉集气系统应设事故用工业水管,集气管操作台上部应设清扫孔。()
煤气净化运行时,净化设施与罗茨风机压差过大异常时,应首先判断设施内有()现象。
煤气净化 罗茨风机:煤气净化工艺与技术.ppt
煤气净化工艺与技术 1.1 煤气净化在炼焦生产中的意义与作用 煤是人类最早利用,而且目前仍然得到最广泛利用的能源之一。人类利用煤炭资源主要有以下方法: ⑴燃烧:将煤直接燃烧以获得热能,如用煤加热食物、加热锅炉生产蒸汽发电等。 ⑵气化:将煤控制在一定条件不完全燃烧以生产煤气,如发生炉煤气、水煤气等。 ⑶液化:将煤在高温高压的条件下进行裂解和精制制取液体燃料,如汽油等。 ⑷干馏:将煤在隔绝空气条件下加热使其分解,生产焦炭、煤气和各种化工产品。 焦炭和煤气是钢铁生产、机械制造和化工合成工业的重要原料和燃料。从煤气中回收的化合物主要有氨、粗苯、硫磺和焦油等。 炼焦化学工业是煤炭的综合利用工业,在煤的各种利用方法中,炼焦工艺对煤的利用程度最高。煤在炼焦时,约有75%左右变成焦炭,另外25%左右则变成煤气和化工产品。 1.2 炼焦生产基本工艺 焦化生产一般由备煤、炼焦、煤气净化和生产辅助设施组成。 备煤车间的任务是为焦炉制备符合炼焦用煤质量要求的煤料。备煤车间一般由卸煤、贮煤、配煤、粉碎等工段及带式输送机等组成。有的焦化厂还有洗煤工段。 炼焦车间是将煤加热炼制成焦炭和煤气。炼焦车间一般由炼焦、熄焦和筛焦(焦处理)工段组成。有的大型焦化厂还建有干熄焦装置。 煤气净化车间是将焦炉生产的粗煤气进行净化并回收化工产品。煤气净化车间一般由冷鼓、脱硫、脱氨、脱苯和污水处理等工段组成。 生产辅助设施包括供水、供电、供汽及产品的检化验等。 1.3 焦化产品生成过程 将煤装入焦炉炭化室后,在隔绝空气的条件下对其进行加热,在高温作用下,煤质逐步发生一系列的物理和化学变化。 装入煤在200℃以下蒸出表面水分,同时析出吸附在煤中的二氧化碳、甲烷等气体。随着温度的升高,煤开始软化和熔融形成胶体状物质(称为胶质层),并分解产生气体和液体。在600℃以前,从胶质层中析出的蒸汽和气体叫做初次分解产物,主要含有甲烷、一氧化碳、二氧化碳、化合水及初次焦油气等,含氢量很低。 温度继续升高,胶质层开始固化形成半焦。挥发物从半焦中逸出,进一步分解形成新的产物,如氮与氢生成氨,硫与氢生成硫化氢,碳与氢则生成一系列的碳氢化合物及高温焦油等。 温度继续升高,随着半焦中的挥发物不断逸出,半焦则收缩并变成焦炭。通常情况下,炭化室中焦炭成熟的最终温度为950~1050℃,焦炭中残余的挥发分含量为1%~2%。 1.4 焦化产品的产率 炼焦生产过程中,焦炭与各种化学产品的产率是随炼焦用煤的质量和炼焦时各种工艺制度的变化而变化的,焦炭与化学产品的产率如下:%(对干煤) 焦炭 75~78 净煤气 15~19 焦油 2.4~4.5 化合水 2~4 粗苯 0.8~1.4 氨 0.25~0.35 硫化氢 0.1~0.5 氰化氢 0.05~0.07 吡啶类 0.015~0.025 1.5 影响焦化产品产率和质量的因素 影响炼焦化学产品产率和质量的因素主要是炼焦煤的质量和焦炉操作的各项工艺制度。 装入炭化室的炼焦煤的质量是决定各种产品产率和质量的主要因素,其中煤料中挥发分含量及煤料中的氧、氮、硫等元素对化学产品的产率和质量的影响最大。 配煤的挥发分高,焦油、粗苯以及煤气的产率就高。煤料中含氧量高,炼焦过程中产生的化合水量就多,炼焦煤的含氮量一般在2%左右。在炼焦过程中,60%左右的氮残存于焦炭中,15%~20%的氮与氢反应生成氨,其余部分则生成氰化氢、吡啶和其他含氮化合物。煤中硫的含量决定了煤气和焦油中硫化物的含量,通常干煤含硫量在0.5%~1.2%,其中20%~45%转入煤气中,配合煤的挥发分越高,炼焦炉温越高,转入煤气中的硫就越多。炼焦煤气的产率主要取决于炼焦煤料的挥发分,挥发分越高,煤气产率就越大。 1.5影响焦化产品产率和质量的因素 在炼焦煤料性质稳定的情况下,炼焦操作及加热制度的变化对炼焦化学产品的质量和产率也有一定的影响。通常情况下,炼焦炉温越高,初次分解产物在与炉墙接触时产生的二次裂解就越多,其结果是焦油中的酚类及中性油类的含量降低,而萘、蒽、沥青和游离碳的含量增加,焦油的密度增大;当二次裂解温度超过800℃时,在苯类产品中,甲苯、二甲苯等产率减少,苯产率增高。此外,炭化室炉顶空间温度过高会造成炼焦化学产品的二次裂解加剧。若由于装煤不满而造成炉顶空间温度在全过程中偏高,则会降低焦油、苯和氨的产率,并增加化合水和氰化物的产率,同时还会造成甲烷和烃类分解,使煤气中的氢含量增加,煤气的热值下降。焦炉的压力制度对炼焦化学产品的产率也产生一定的影响。炭化室内的压力大,增大了煤气泄漏的可能,炭化室内负压则会吸入空气,部分化学产品在炭化室内被烧掉,结果是煤气的数量与质量均会发
煤气净化 罗茨风机:煤气净化技术方案
煤气净化技术方案
工艺技术选择
煤炭提质工艺产生的煤气,其净化工艺采用的主要技术包括:煤气的冷凝冷却及排送、焦油氨水分离、焦油、萘、硫化氢、氰化氢、氨等杂质的脱除以及粗苯的回收。
1、煤气的冷凝冷却
(1)高效横管间冷工艺
煤气高效横管间冷工艺。其特点是:煤气冷却效率高,除萘效果好;当煤气温度冷却至20~22℃,煤气出口含萘可降至0.5g/m3,不需另设脱萘装置即可满足后续工艺操作需要。
高效横管间冷工艺通常分为二段式或三段式初冷工艺。当上段采用循环冷却水,下段采用低温冷却水对煤气进行冷却时,称为二段式初冷工艺。为回收利用荒煤气的余热,通常在初冷器上部设置余热回收段,即构成三段初冷工艺。采用三段初冷工艺,回收的热量用作冬季采暖或其它工艺装置所需的热源,不仅可以回收利用煤气的余热,同时也可节省大量循环冷却水,节能效果显著。
(2)间直冷工艺
煤气的冷凝冷却也可采取先间冷,后直冷的“间直冷工艺”对煤气进行冷却。间直冷工艺的优点在于煤气在通过直冷塔冷却的同时,可对煤气中夹带的煤粉进行洗涤、净化,使去后续装置的煤气更加洁净;缺点是工艺流程较长,运行费用高,脱萘效果差,一般需单独设置后续脱萘装置。
2、焦油氨水的分离
焦油氨水的分离采用“混合分离工艺”,即从煤气管道气液分离器下来的焦油氨水混合液与初冷器下来的煤气冷凝液混合后,进入焦油氨水分离器内进行分离的工艺。目前,普遍采用的焦油氨水分离工艺有“卧式槽分离工艺”及“立式槽分离工艺”两种。
“卧式槽分离工艺”即传统采用的机械化氨水澄清槽式分离工艺;“立式分离工艺”即焦油氨水混合物首先经机械刮渣槽分出颗粒较大的焦油渣,然后进入立式焦油氨水分离槽内进行焦油氨水分离的工艺。生产实践表明,上述两种分离工艺均能达到工艺分离要求。
同卧式分离工艺相比,立式分离工艺中焦油氨水的分离效果要更好一些;同时,焦油氨水分离槽采用夹层式设计结构,分出的热氨水直接进入外层作为内层焦油保温所需的热介质,节省了由传统蒸汽保温所造成的热能消耗。
3、煤气中焦油雾的脱除
煤气中焦油雾的脱除采用电捕焦油器工艺完成。该工艺可将煤气中的焦油含量脱除到20mg/m3以下。
电捕焦油器通常设置在煤气鼓风机前,以防止煤气经鼓风机升温后煤气焦油中的萘挥发至煤气中,而使煤气中萘含量升高。
电捕焦油器沉淀极所采用的结构形式通常有管式及蜂窝式两种;由于蜂窝式结构形式排列紧凑、设备截面利用效率高,因而成为高效电捕焦油器所采用的沉淀极的主要结构形式,得到普遍采用;此外,为保证电捕焦油器电流操作性能的稳定,采用恒流电源新技术取代传统的硅整流器技术。
4、煤气脱硫
煤气采用的脱硫方法有AS法、真空碳酸盐法、乙醇胺法等吸收法脱硫工艺;以及HPF法、FRC法、ADA法等氧化法脱硫工艺。
(1)AS法、真空碳酸盐法、乙醇胺法等吸收法脱硫工艺,通常可将煤气中的硫化氢脱至200~500mg/m3;脱硫富液经解吸再生,产生出含有硫化氢的酸性气体;该酸性气体可采用接触法制取硫酸或采用克劳斯法制取硫磺。
吸收法脱硫工艺的特点是:无废液或废液量很少,酸汽后处理工艺相对简单、可靠,但其脱硫效果不能满足行业脱硫标准硫化氢含量≤300mg/m3的要求。
(2)湿式氧化法脱硫工艺,脱硫脱氰效率高,通常可将煤气中的硫化氢脱至100mg/m3以下;富液经氧化再生,生成单质硫及硫化物盐类。对采用以氨为碱源的湿式氧化法脱硫工艺(如FRC法、HPF法等),可采用废液焚烧工艺对生成的单质硫及硫化物盐类进行焚烧处理,制取硫酸;对采用以钠为碱源的湿式氧化法脱硫工艺(如ADA法等)对生成的单质硫可经熔硫后外销,或将过滤出的硫膏直接外销。废液则采用提盐或还原热解工艺加以处理。
(3)HPF湿式氧化法脱硫工艺以煤气自身含有的氨为碱源,HPF为催化剂,具有脱硫效率高(脱硫可达98%,脱氰可达80%),投资省、运行成本低、易于操作等优点,因而在行业内应用广泛,具有较好的发展前景。但该脱硫工艺目前尚不够完善,存在的问题主要是:
脱硫过程中产生NH4SCN和(NH4)2S2O3等副盐类缺乏有效的处理工艺;当脱硫液中盐类浓度积累较高时,严重影响脱硫效率,废液外排又会造成环境污染;生成的单质硫纯度低、质量差、销售困难。
(4)国产化真空碳酸钾法脱硫工艺特点是:与煤气初冷工艺结合,直接高效利用荒煤气余热用于富液解吸;吸收和解吸采用两段法,以提高脱硫效率,塔后硫化氢可脱至200mg/m3或更低。此外,由于真空碳酸钾法脱硫工艺配置在煤气净化工艺流程的最末端,脱硫液再生后产生的硫化氢酸汽浓度高、杂质少,可采用湿式或干式接触法工艺制取98%硫酸,用做焦化厂硫铵装置生产硫酸铵的原料或外销;也可采用克劳斯工艺制取元素硫,其纯度可达99%以上。
净化工艺流程
1、鼓冷工段
(1)工艺流程
煤气在集气管被循环氨水喷洒冷却至70~80℃后,沿吸气管经气液分离器进入直冷塔;氨水由直冷塔上部喷淋,下部带有煤焦油的氨水进入冷环水槽;煤气由直冷塔下部进入,上部排出进入间冷器;将煤气冷却到40~45℃。煤气经电捕焦油器后进入罗茨鼓风机加压,煤气送回回转炉做燃料、外供煤气送脱硫工段。
从气液分离器出来的煤焦油氨水,自流入热环水槽静置分离煤焦油,从直冷洗涤塔出来的煤焦油氨水,自流入冷环水槽静置分离煤焦油,煤焦油经煤焦油中间槽后用泵送至煤焦油贮槽脱水,热循环氨水用泵送至炉集气管循环使用;冷循环氨水送至直冷洗涤塔循环使用。
从间冷器出来的焦油氨水,自流入冷环水槽静置分离煤焦油,焦油用泵送至焦油贮槽脱水,冷循环氨水用泵送至间冷器循环使用。
从焦油贮槽脱水后的焦油(水分<4%)经焦油泵后外送。
(2)工艺特点:
①投资小,便于操作;
②煤气中焦油去除率高;
③采用两段直、间冷循环水,符合块煤干馏回收焦油的工艺特点;
④技术成熟,在生产中已有应用。
2、脱硫工段
(1)工艺流程
来自鼓冷工段的煤气进入脱硫塔,与塔顶喷淋下来的脱硫液逆流接触,经洗涤后的煤气H2S含量小于200mg/Nm3,脱硫煤气进捕雾段除去雾滴后送至煤气柜。
吸收了H2S的脱硫液从脱硫塔底流出,经液封槽进入反应槽(溶液循环槽),经补充从催化剂贮槽滴加催化剂溶液后,用循环泵送到溶液加热器,使溶液保持在35℃左右进入再生塔;同时从再生塔底部通入压缩空气和脱硫富液,使溶液在塔内得以氧化再生。再生后的脱硫液返回脱硫塔顶循环喷淋脱硫。
再生塔浮选出的硫磺泡沫,利用位差自流到硫泡沫槽,再由硫泡沫泵加压后送连续熔硫釜,用蒸汽加热使硫熔融,并与清液分离,清液入溶液缓冲槽降温后由液下泵送至溶液循环槽循环使用,得到的硫放至冷却盆,冷却后外售。
(2)工艺特点:
①采用煤气中自身含有的氨为碱源,以PDS加栲胶为复合催化剂。具有脱硫效率高、基建投资省、运行稳定和操作费用低等特点。
②脱硫塔采用高效且比表面积大的新型填料。
3、气柜及加压站工段
(1)工艺流程
由脱硫工段来的煤气经过气柜前煤气水封进入气柜储存,再经煤气加压风机供甲烷化合成车间。
(2)工艺特点:
进入水封前管道上安装有煤气气动调节阀与流量计构成一个调节回路,通过外送煤气用户的使用量调节气动阀的开度,使流量计保持一定值,气柜高低报警与煤气加压机连锁,并且净化车间罗茨风机的停止信号与煤气加压机连锁用以保证系统安全稳定运行。气柜三塔间水封,由氨水泵房自吸泵由氨水池抽送,水封多余氨水流回氨水水池,形成循环,间歇补水。冬季为防止水封冰冻,设置蒸汽加热管道。
煤气净化 罗茨风机:煤气净化设施从罗茨风机入口端至电炉煤气净化设施为负压运行段。()
直流牵引电机采用换向极是为了改善换向性能。 正确。 错误。
转炉煤气是一种有恶臭味的有毒气体。() 正确。 错误。
脉流牵引电机刷架圈的功用是固定补偿绕组。 正确。 错误。
在完成团队成员的初步选择、评估后,通常还要进行团队成员组合的匹配性分析,这种分析通常应从()等方面进行分析。 正确。 错误。
车体和转向架间的连接装置,既是承载装置,又是牵引装置,还起到车体和转向架之间的活动关节作用。 正确。 错误。
煤气净化设施从罗茨风机入口端至电炉煤气净化设施为负压运行段。()
罗茨鼓风机费用 罗茨鼓风机图片 沈阳罗茨鼓风机
山东锦工有限公司
地址:山东省章丘市经济开发区
电话:0531-83825699
传真:0531-83211205
24小时销售服务电话:15066131928
