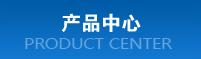

风电叶片ss面与ps面图_罗茨风机
风电叶片ss面与ps面图:一种风电叶片后缘立面区域填充方法与流程
本发明涉及风电叶片结构领域,尤其涉及一种风电叶片后缘立面区域填充方法。
背景技术:
风电叶片后缘中间部分是有一定厚度的立面,此立面在模具上体现为凹槽。在此区域,叶片内部空腔间隙较大,部分位置超过理论合模间隙。合模间隙是直接影响叶片外轮廓形态、合模胶用量、叶片重量等的重要指标,合模间隙大会导致合模胶厚度超差,降低粘接强度,这就需要精确控制叶片合模间隙。
为了调节此处的合模间隙,目前一般是使用玻纤布填充或制作粘接角。若使用玻纤布填充该区域,一方面层铺、灌注困难,容易出现褶皱、干纤维等缺陷,影响粘接质量和生产效率;另一方面易导致叶片超重等问题,改变叶片后缘力学性能。若制作粘接角,由于空腔结构窄扁、空间狭小,所以一方面制作工艺较为复杂,不易成型,另一方面粘接角容易褶皱、塌陷,需要返工。
同时,此区域在模具上为凹槽,层铺时壳体玻纤布容易出现悬空现象,真空灌注后则形成富树脂,降低叶片力学性能,影响叶片的强度和使用寿命。
技术实现要素:
本发明的目的在于提供一种结构简单、操作便捷的风电叶片后缘立面区域填充方法。
为实现上述目的,本发明的一种风电叶片后缘立面区域填充方法的具体技术方案为:
一种风电叶片后缘立面区域填充方法,包括以下步骤:在铺设壳体外蒙皮前,在ss面和ps面壳体后缘立面的对应位置上铺设包覆层;在模具凹槽处铺设多个垫块,将后缘凹槽处填平,并与模具凹槽立面贴实;依次铺设壳体外蒙皮、单向布、壳体芯材、壳体内蒙皮,完成整个壳体的铺层工序;进行辅材铺设、真空灌注及预固化、辅材清理、试合模、合模胶刮涂工序处理;翻转合模,通过合模胶将ss面壳体和ps面壳体粘接固定在一起。
进一步,包覆层为两层双轴布,铺设于叶片后缘立面处的模具凹槽表面。
进一步,铺设包覆层时,在弦向方向上两层双轴布的一侧均超出分型线的翻边,另一侧与后缘分型线间距均宽于垫块的宽度。
进一步,两层双轴布的另一侧与后缘分型线间距分别为垫块的宽度多出9.5~10.5cm和多出4.5~5.5cm。
进一步,采用两层玻纤布的包覆层按照先大后小的顺序铺设,玻纤布与模具面紧密贴实。
进一步,多个垫块之间采用树脂钉固定连接在一起。
本发明的一种风电叶片后缘立面区域填充方法的优点在于:
1)结构设计简单合理,操作便捷,生产效率高;
2)避免了层铺时此处玻纤布悬空现象,从而消除了富树脂缺陷,提高了叶片质量;
3)能够有效地调节叶片后缘立面区域的合模间隙,消除了此区域厚度超差问题,提高粘接强度;
4)减少合模胶用量,降低叶片重量,提高叶片后缘气动性能,增加叶片的强度和使用寿命。
附图说明
图1为本发明的填充结构在风电叶片中的截面图。
图中:1、垫块;2、包覆层;3、壳体外蒙皮;4、单向布;5、壳体芯材;6、壳体内蒙皮;7、合模胶。
具体实施方式
为了更好的了解本发明的目的、结构及功能,下面结合附图,对本发明的一种风电叶片后缘立面区域填充方法做进一步详细的描述。
如图1所示,其示为本发明的一种风电叶片后缘立面区域填充方法,用于调节叶片后缘立面区域的合模间隙,填充方法包括:
首先,在铺设壳体外蒙皮3前,在ss面和/或ps面壳体后缘立面的对应位置上铺设包覆层2。
具体来说,包覆层2为两层双轴布,铺设于叶片后缘立面处的模具凹槽表面,将后述的垫块1包覆。并且,当铺设包覆层时,在弦向方向上两层双轴布的一侧均超出分型线的翻边,另一侧与后缘分型线间距均宽于垫块1的宽度,优选两层双轴布与后缘分型线间距分别为垫块1的宽度多出9.5~10.5cm(优选10cm)和多出4.5~5.5cm(优选5cm)。两层玻纤布的包覆层2按照先大后小的顺序铺设,玻纤布与模具面紧密贴实,以保证平整无褶皱,提高粘接质量和生产效率。
进一步,在模具凹槽处铺设多个垫块1,将后缘凹槽处填平,并与模具凹槽立面紧密贴实在一起。
具体来说,垫块1与包覆层2组成叶片后缘立面区域填充结构,用于控制后缘合模间隙和刮胶厚度,通过上述方法操作,能够防止形成富树脂,提高了叶片质量。并且,多个垫块1采用树脂钉固定连接在一起,防止偏移。其中,本发明中垫块1优选采用制作叶片的pvc泡沫芯材,但并不仅限于采用pvc泡沫芯材。根据理论后缘截面设计垫块1,垫块1的实际尺寸参照试合模的合模间隙调节,在合模间隙超差较小处,可以只在模具有凹槽的一侧填充垫块1。
进一步,按工艺依次铺设壳体外蒙皮3、单向布4、壳体芯材5,壳体内蒙皮6等,完成整个壳体铺层工序。
进一步,根据叶片制作工艺,进行辅材铺设、真空灌注及预固化、辅材清理、试合模、合模胶刮涂等工序处理。
进一步,翻转合模,合模胶7将ss面壳体和ps面壳体粘接在一起,合模胶厚度符合设计要求,提高粘接强度。
需要说明的是,本发明以在两个面均放置垫块1为例,但并不限于上述方案。
本发明一种风电叶片后缘立面区域填充方法,结构设计简单合理,操作便捷,生产效率高;避免了层铺时此处玻纤布悬空现象,从而消除富树脂缺陷,提高了叶片质量;能够有效地调节叶片后缘立面区域的合模间隙,消除此区域厚度超差问题,提高粘接强度;减少合模胶用量,降低叶片重量,提高叶片后缘气动性能,增加叶片的强度和使用寿命。
以上借助具体实施例对本发明做了进一步描述,但是应该理解的是,这里具体的描述,不应理解为对本发明的实质和范围的限定,本领域内的普通技术人员在阅读本说明书后对上述实施例做出的各种修改,都属于本发明所保护的范围。
风电叶片ss面与ps面图:叶片制造工艺简介.ppt
风轮叶片 风轮叶片 SS面与PS面的合模 开启PS面的真空泵,抽真空5min后翻转PS模具合模,并扣上全部搭扣。然后关闭真空泵剪开真空袋,观察叶根的粘接情况,将挤出的结构胶刮除干净,缺胶的位置用刮板补上结构胶。 合模 糊制内部粘接带 叶片前缘-0.1m到10.5m,后缘-0.1m到5.5m的合模缝处需要用手糊环氧树脂(E700+H735=100∶35,重量比,手糊8层双轴向玻纤布作为内部粘接带, 粘接带以合模线中心对称。手糊时四层作为一个整体。 叶片后固化脱模及转运 升温开始后用棉被将叶根挡住,将温度升到70℃后保温7小时后关闭加热系统。掀开棉被,根部用电风扇吹风散热,当温度低于50℃时,开启翻转机构,转动PS模具落回地面。 1. 法兰边切割与打磨 2 .叶片定位准备根部切割、打孔 1 将叶片运到切割打孔工位。 2 在叶片根部2m及中部23m处用吊带和行车吊起,缓慢放在打孔机的3个支撑板上,使叶根1m处位于第一个支撑板上,叶尖吊垂线恰好在事先画好的定位圈里,调节吊带使得叶片与支撑板无间隙,则定位准确,否则缓慢调节吊带使得定位准确。此时叶片根部合模缝角度约9度。 3.根部切割、打孔 注意: 1 打孔机操作要严格遵守操作指导书和注意事项,避免损坏打孔机。 将右侧合模线下方第二个孔计做序号1。 3 在用数显水平尺时要确认其正常使用。 4 在试打孔时要质检员确认,如果合格,方可进行打孔,如果不行就要调试打孔机的位置,然后在试打孔,合格之后再打孔,如果不合格,继续上述步骤。 4 .T型螺栓装配 清理干净螺孔周边的毛刺。 将圆螺母用橡皮锤轻敲放入装入64mm的孔径的横向螺孔,序号15的孔要放入端面带内螺纹的圆螺母。圆螺母待倒角的螺孔对准纵向孔。如果螺母很难进入,则用粗砂纸打磨空内壁,使孔径稍微变大,再放入圆螺母,将定位工装螺杆装入横螺母的螺纹中用扳手拧紧。 将长螺杆插入纵向孔内,拧入圆螺母,将密封圈压入长螺杆与纵向孔之间的间隙。 用检测样板检测长螺杆的位置是否准确。如果有长螺杆无法穿过检测样板,则调整圆螺母和螺杆,使其能够套入检测样板。 5. 糊制根部环向粘接带 1 清理干净螺孔周边的脱模布和灰尘。 2 在螺栓与叶片内,外有台阶的地方刮涂胶粘剂(WD3135:WD3134=100:45,重量比),使横螺母与内外表面台阶平滑过渡。 3 在横向孔的内外表面需要 手糊环氧树脂(E700+H765=100:35)糊制3层双轴向布。 6. 糊制外部粘接带 1 撕掉前缘0m到5 m及后缘0m到8.5m的合膜缝上下各200mm脱模布。 2 用结构胶(WD3135:WD3134=100 :45,重量比)补平合模缝处缺胶缝隙。 3 在前缘0m到5 m及后缘0m到8.5m的外部用手糊环氧化树脂(E700+H735=100:35,重量比)手糊8层双轴向玻纤布作为外部粘结带,粘接带以合模线中心对称,每层都从叶根0m处开始。 7. 安装32孔径的轴向螺栓 1 待根部环向粘接带完全固化后卸掉定位工装。 2 将密封圈套入长螺杆后,把长螺杆插入径向孔径中,用六角螺母将其拧紧,使其在孔外的长度为209mm。 8.叶片壳体打磨 用打磨机配套使用80目的砂纸进行打磨,打磨叶片壳体撕掉脱模布留下的细小毛刺、脱模布留下的粗糙布纹以及残留的脱模剂成分。 9. 安装人孔盖外环部分 1 清除掉叶跟部的杂物及灰尘使其尽量平整干净。从叶跟部量取1000mm画线做好标记。 2 将人孔板用约10mm厚的木块垫紧固定在画好的标记线上,然后用结构胶(WD3135:WD3134=100 :45,重量比),填平缝隙。 3 在其与叶片的连接处的两边用环氧树脂手糊200mm宽的双轴向玻纤布2层(E700+H735=100:35,重量比) 10.第一遍喷漆 1用压缩空气将叶片表面吹干净。 2将油漆与固化剂、稀释剂按100:4:0.2~0.8的比例准确均匀混合。 3两人配合用高压混气喷枪从根部向叶尖匀速均匀的喷涂,喷涂完毕后立即清洗喷枪。 11. 第一遍喷漆表面固化后补腻子 待油漆固化后,在基材有缺陷处如针孔、凹痕等处刮腻子修补. 刮腻子时刮板与叶片呈45°,
风电叶片ss面与ps面图:四、叶片解剖测量、取样实验 后缘辅梁(UD):PS 面辅梁与外蒙皮结合完全,只是 在断裂后与壳体产生抽离。SS 面后缘辅梁在 L6m 处折断。 跟着风力发电范围和技巧的赓续成长,风电机组大年夜型 化.
四、叶片解剖测量、取样实验
后缘辅梁(UD):PS 面辅梁与外蒙皮结合完全,只是 在断裂后与壳体产生抽离。SS 面后缘辅梁在 L6m 处折断。
跟着风力发电范围和技巧的赓续成长,风电机组大年夜型 化趋势越来越明显。而叶片长度的增长,在增大年夜风能捕获效 率的同时,也增大年夜了叶片段裂破坏的概率。平日叶片产生断 裂的重要原因包含临盆过程中工艺控制不良,叶片根部局部 区域树脂固化不完全导致的强度、刚度降低,风速超限,风 电机组掉速,电气故障以及雷击等。本文针对某风电场机组 叶片段裂变乱,从风速超限、电气故障、雷击、临盆工艺等 方面进行深刻分析,肯定了叶片段裂掉效原因。
叶片段裂变乱概述
叶根地位:叶根避雷导线于 L2m 处断开并掉踪。
后缘粘接:叶根外部自 L6m 至 L15.5m 处后缘开裂, 自 SS 面 L32m 至叶尖开裂。
粘接处未产生分别,前 缘粘接厚度及宽度无法测量。 腹板粘接:全部腹板粘接面未产生剥离,因叶片折断 导致叶根部位粘接胶与主梁剥离。不雅察叶片内部,腹板未发 生胶层开裂现象。 叶尖部分:铝叶尖全部甩出损掉,叶尖部位 33m 至叶 尖部分碎裂。
某风电场 6# 风电机组于 2020 年 2 月 25 日 0 时 32 分 阁下因叶片段裂停机。叶片型号:##96-2000/A5,叶片编号: 1201-149;叶片套号:097;制造时光:2012 年 8 月 12 日。 叶片段裂初始折断地位:叶片前缘 L4.5m 至后缘 L6m,其 他折断地位断定为二次断裂点。
根据对叶片的整体检查成果,未发明明显的雷 击陈迹。经现场勘查,叶尖地位的碎裂为叶片坠落时的二次 毁伤。 主梁部分:PS 和 SS 面主梁均自叶根 L2.5m 处与蒙皮分别,主梁部分整体保存完全。PS 面与 SS 面主梁与蒙皮均 结合优胜。经现场勘查,主梁处的折断是因为叶片段裂掉效 后,因重力感化导致的主梁与壳体产生分别,主梁本身并未 断裂。
芯材及蒙皮:叶根处、前缘 L12m 处、后缘 L13m 处均 扯破露出 PVC 芯材,残存 PVC 芯材注解粘接无异常。经现 场勘察,芯材和蒙皮处均为扯破,这是因为叶片在断裂后受 重力影响,导致蒙皮与芯材产生扯破
经由过程一一分析导致叶片掉效的各类外部身分对叶片掉 效的影响,剖断叶片掉效的原因。导致叶片掉效的外部影响 身分及剖断办法如表 1 所示。
一、变乱产生时风电机组状况分析 根据 SCADA 监控体系信息,在变乱产生前后,发明 6# 风电机组异常,经由分析数据库内 1s 数据(见表 2),
曲折实验是将必定外形和尺寸的试样放置于曲折装配 上,以规定直径的弯心将试样曲折到请求的角度后,卸除 实验力,检查实验遭受的变形机能(因为样品 A 尺寸较小 且缺点过大年夜,导致实验机无法做力学机能测试,是以,本 次力学机能实验用样块 B 和 C 做比较测试)。由曲折实验 数据(表 5)可知,缺点样块的曲折强度仅为正常样块弯 曲强度的 67.97%;而曲折模量比正常样块大年夜 9.13%。曲折强度降低,使得辅梁的抗剪切才能严重降低;而曲折模量 值越大年夜,表示材料在弹性极限内抵抗曲折变形才能相对越 小,实验数据注解辅梁出现褶皱后,降低了本身的抗变形 才能。
叶片产生断裂变乱后,3支叶片均正常顺桨且保持同步,具体过程见图 4。
变乱现场细节描述
二、变乱产生时风速及转速分析
根据汗青数据,2020 年该风电机组的最大年夜风速为 24.3m/s,未跨越设计风速。叶片段裂前后,风速未跨越极 限风速,2020 年 2 月 25 日 0 时 30 分至 0 时 40 分的最大年夜风速为 15.5m/s,处于正常运行风速范围内。
(1)叶根处存在 2 处褶皱:叶根 L2.5m 处轴向褶皱 (L=600mm,W=32mm,H=8mm,高宽比为 0.25);叶根 L1.8m 处轴向褶皱(L=480mm,W=27mm,H=6mm,高宽 比为 0.22)。因为叶根 L2.5m 折断截面并未发明褶皱分层, 且 L2.5m 折断截面呈弦向折断与 2 处轴向褶皱没有直接关 联,剖断 2 处褶皱均为质量缺点。
由图 3 可知,叶片产生断裂时,机舱振动较大年夜,最大年夜 值达到 3.4mm 阁下,风电机组持续摆振约 2 分钟,之后振 幅逐渐减小。
三、雷击分析
变乱现场调研及分析
前缘粘接:前缘粘接角保存完全,自 L4.5m 处产生一 次断裂;自 L7m 处产生二次折断。
由图 5 可知,在叶片段裂前的一小段时光内,机舱风 速仪所测得的风速切变尚可,未出现较快的风速变更。该 风电机组在叶片段裂变乱产生前后的最大年夜转速为 17.42rpm (2020 年 2 月 25 日 0:32:02),未产生超速。
如雷电对电网或风电机组冲击较大年夜,应出现短时光的 体系过电压;如雷电冲击能量较小,可能仅导致叶片破坏而 无法引起体系过电压。由变乱前后体系电压变更情况图(图 6)可知,叶片段裂前后体系电压无明显波动。
综合分析可知:(1)清除故障时风速跨越设计值导致 叶片段裂的可能;(2)清除风电机组飞车的可能;(3)清除雷击身分导致叶片段裂的可能。
叶片出现断裂的时光为 2020 年 2 月 25 日 0 时 32 分 32 秒。
叶片各截面测量明细见表 3,发明的重要缺点见表 4。
综合分析如下:
(2)后缘 L23m 和 L24m 处的断面上均发明有空胶现 象,叶片局部空胶风险较小,可以清除。
(3)抽检了 10 处叶片后缘粘接厚度,存在 4 处超标, 部分胶层存在空胶现象。除后缘 L8m 地位超标严重(超标 275%)外,其余 3 处最大年夜超标为 16.67%。但胶层超厚的缺 陷并未在叶片初始断口地位,是以,后缘胶层缺点不克不及作为 本次叶片段裂变乱的重要原因,可以清除。
(4)L6m 处 后 缘 辅 梁(UD) 弦 向 褶 皱, 长 度 为 320mm,宽度为 25mm,高度为 5mm,高宽比为 0.20。叶 片在 L6m 处产生折断,现场勘查发明 L6m 折断截面存在褶 皱分层的现象,弦向褶皱对叶片折断的影响身分很大年夜,初步 剖断该缺点是造成叶片折断的重要身分。
剖断该缺点是造成叶片折断的重要身分。
结合实验数据分析可知:缺点样块的曲折强度仅为正 常样块曲折强度的 67.97%;褶皱缺点导致辅梁抗拉强度下 降了 9.18%;而曲折模量比正常样块大年夜 9.13%;以上数据充 分辩明,叶片 L6m 处的后缘辅梁(UD)弦向褶皱是造成叶 片折断掉效的重要诱发身分。
五、辅梁弦向褶皱材料力学机能测试、拉伸测试 因叶根外部自 L6m 至 L15.5m 处后缘开裂,在辅梁褶 皱地位取三个样块:第一块为 L6m 处后缘辅梁断口地位样 块,标记为 A 样块;第二块为 L7.5m 处后缘辅梁弦向 45° 褶皱样块,标记为 B 样块;第三块为正常状况的辅梁,标 记为 C 样块,作为比较样块。
拉伸实验是检测强度和刚度最重要的实验办法之一, 经由过程拉伸实验可以不雅察材料的变形行动。由表 6 可知,褶皱 缺点导致辅梁抗拉强度降低了 9.18%。
结论
综合分析,该变乱风电机组叶片的掉效过程是由叶片 L6m 处后缘辅梁(UD)弦向褶皱诱发叶片开端断裂,叶片 在离心力的感化下,蒙皮及主梁产生撕扯分层开裂,在叶片 开裂后,叶片稳定性大年夜幅降低,当叶片载荷传递到根部后, 因根部构造强度较大年夜,在叶片 L6m 处应力积聚,导致后缘 L6m 处由内向外扯破,迎风面和背风面主梁折断,进而导 致叶片刹时掉效。
(作者单位:中国电建集团中南勘测设计研究院有限公司)
风电叶片ss面与ps面图:某风电场机组叶片断裂原因分析
北极星风力发电网讯:随着风力发电规模和技术的不断发展,风电机组大型 化趋势越来越明显。而叶片长度的增加,在增锦工能捕获效 率的同时,也增大了叶片断裂损坏的概率。通常叶片发生断 裂的主要原因包括生产过程中工艺控制不良,叶片根部局部 区域树脂固化不完全导致的强度、刚度降低,风速超限,风 电机组失速,电气故障以及雷击等。本文针对某风电场机组 叶片断裂事故,从风速超限、电气故障、雷击、生产工艺等 方面进行深入分析,确定了叶片断裂失效原因。
叶片断裂事故概述
某风电场 6# 风电机组于 2020 年 2 月 25 日 0 时 32 分 左右因叶片断裂停机。叶片型号:##96-2000/A5,叶片编号: 1201-149;叶片套号:097;制造时间:2012 年 8 月 12 日。 叶片断裂初始折断位置:叶片前缘 L4.5m 至后缘 L6m,其 他折断位置判断为二次断裂点。
事故现场细节描述
叶根位置:叶根避雷导线于 L2m 处断开并失踪。
后缘粘接:叶根外部自 L6m 至 L15.5m 处后缘开裂, 自 SS 面 L32m 至叶尖开裂。
前缘粘接:前缘粘接角保存完整,自 L4.5m 处发生一 次断裂;自 L7m 处发生二次折断。
粘接处未发生分离,前 缘粘接厚度及宽度无法测量。 腹板粘接:整个腹板粘接面未发生剥离,因叶片折断 导致叶根部位粘接胶与主梁剥离。观察叶片内部,腹板未发 生胶层开裂现象。 叶尖部分:铝叶尖全部甩出丢失,叶尖部位 33m 至叶 尖部分碎裂。
根据对叶片的整体检查结果,未发现明显的雷 击痕迹。经现场勘查,叶尖位置的碎裂为叶片坠落时的二次 损伤。 主梁部分:PS 和 SS 面主梁均自叶根 L2.5m 处与蒙皮分离,主梁部分整体保存完整。PS 面与 SS 面主梁与蒙皮均 结合良好。经现场勘查,主梁处的折断是由于叶片断裂失效 后,因重力作用导致的主梁与壳体发生分离,主梁本身并未 断裂。
后缘辅梁(UD):PS 面辅梁与外蒙皮结合完整,只是 在断裂后与壳体发生抽离。SS 面后缘辅梁在 L6m 处折断。
芯材及蒙皮:叶根处、前缘 L12m 处、后缘 L13m 处均 撕裂露出 PVC 芯材,残存 PVC 芯材表明粘接无异常。经现 场勘察,芯材和蒙皮处均为撕裂,这是由于叶片在断裂后受 重力影响,导致蒙皮与芯材发生撕裂
事故现场调研及分析
通过逐一分析导致叶片失效的各种外部因素对叶片失 效的影响,判定叶片失效的原因。导致叶片失效的外部影响 因素及判定方法如表 1 所示。
一、事故发生时风电机组状态分析 根据 SCADA 监控系统信息,在事故发生前后,发现 6# 风电机组异常,经过分析数据库内 1s 数据(见表 2),
叶片出现断裂的时间为 2020 年 2 月 25 日 0 时 32 分 32 秒。
由图 3 可知,叶片发生断裂时,机舱振动较大,最大 值达到 3.4mm 左右,风电机组持续摆振约 2 分钟,之后振 幅逐渐减小。
叶片发生断裂事故后,3支叶片均正常顺桨且保持同步,具体过程见图 4。
二、事故发生时风速及转速分析
根据历史数据,2020 年该风电机组的最锦工速为 24.3m/s,未超过设计风速。叶片断裂前后,风速未超过极 限风速,2020 年 2 月 25 日 0 时 30 分至 0 时 40 分的最锦工速为 15.5m/s,处于正常运行风速范围内。
由图 5 可知,在叶片断裂前的一小段时间内,机舱风 速仪所测得的风速切变尚可,未出现较快的风速变化。该 风电机组在叶片断裂事故发生前后的最大转速为 17.42rpm (2020 年 2 月 25 日 0:32:02),未发生超速。
罗茨鼓风机选型计算 罗茨鼓风机弹性接头 三叶罗茨鼓风机生产
山东锦工有限公司
地址:山东省章丘市经济开发区
电话:0531-83825699
传真:0531-83211205
24小时销售服务电话:15066131928
